Transporting, handling and storing rubber conveyor belts
Safety
Conveyor belts are packaged in rolls that can be of considerable size and weight. It is therefore essential to maintain the highest safety standards and vigilance to avoid danger to human life and the destruction of goods during their loading, transportation, unloading and storage. Before loading and unloading, always check that the protective packaging and handling elements integrated into the roll are not damaged and make sure that proper and adequate equipment is used throughout the process. For stability purposes, the height of a belt roll should not be higher than three times the width of the belt.
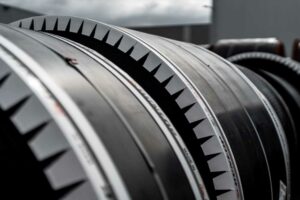
Transportation
Despite their strong construction and durability, rubber conveyor belts can still be damaged during transit due to incorrect handling. At Dunlop, we help minimise the risk by providing one or more of four different kinds of high-grade protective packaging for multi-ply belts – edge protection, plastic foil, wooden drums, and steel reels. Very strong strapping is also used to prevent the belt from unrolling.
The belts are rolled using cores made of wood, steel or plastic with a square hole in the centre for mounting. The diameter of the reel and the hole for the core depends on the weight, width and physical properties of the rolled-up belt. The standard core sizes for both wood and plastic cores are 250mm with a shaft hole square of 110mm and 400mm with a draft hole square of 190mm. Before transportation, the belt reel should be properly secured to avoid excessive movement caused by motion that could damage the vehicle, the belt or pose a health & safety risk.

Lifting
The recommended method for lifting rolls is to insert a steel centre hole. Slings, steel cables or chains suspended from a crane/hoist with a beam should be used for fastening. The distance between the fastening points of the steel core sling should be longer than the width of the belt in order to avoid damage to the belt edges.
The manufacturer/supplier should always provide the dimensions and gross weight of each roll or drum and these should always be within the capacity of the equipment to be used to off-load and move the belt on site. When off-loading, always use skids, forklift truck or crane. Never drop the roll or roll it off the transporter.
Storage
There are a several factors that can have a detrimental effect on belting when stored. It is preferable that belts are stored in the manufacturer’s packing and in an upright position until required for use. Whether stored indoors or outdoors, the ideal storage temperature should be within the range of 10 – 20°C. Prolonged exposure to temperatures below 4°C or in excess of 30°C should be avoided. Although all Dunlop belts are fully resistant to the damaging effects of ground-level ozone and ultraviolet light, a great many belts on the market, especially those imported from Asia, have no resistance at all. Although packaging materials such as wooden drums, foil and cardboard do provide some protection, exposure to ozone, sunlight and/or fluorescent light is best avoided because it can begin to degrade rubber within a very short space of time.
Contact with all types of liquids, especially oils, solvents and corrosive liquids should also be avoided. It is recommended that belts stored outdoors be placed on pallets and positioned on a solid, even surface so that they are not in contact with the ground in order to protect them against damage caused by water, mud, gravel, etc. Additionally, rolls should not stand on the edge or lean against a wall.
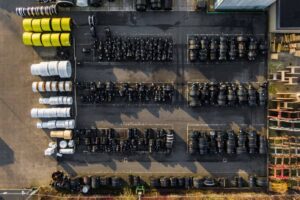
Finally, it is advisable to rotate the belt 90° every 6 months to avoid a constant flex or bend at a single point. There is no need to do this with Steelcord belts that are packed using steel reels which effectively suspend the belt in midair.
Les Williams