A bigger price to pay
The laboratory, situated in our Drachten plant in The Netherlands, lies at the very heart of everything we do in Fenner Dunlop. Having built an unrivalled reputation for quality and product innovation over the past 100 years, the laboratory plays a pivotal role in the quality control process, research & development. For example, it is here that every single batch of rubber compound is checked and thoroughly tested before it is allowed to be used to produce conveyor belts. This is key to achieving consistency of quality and performance.
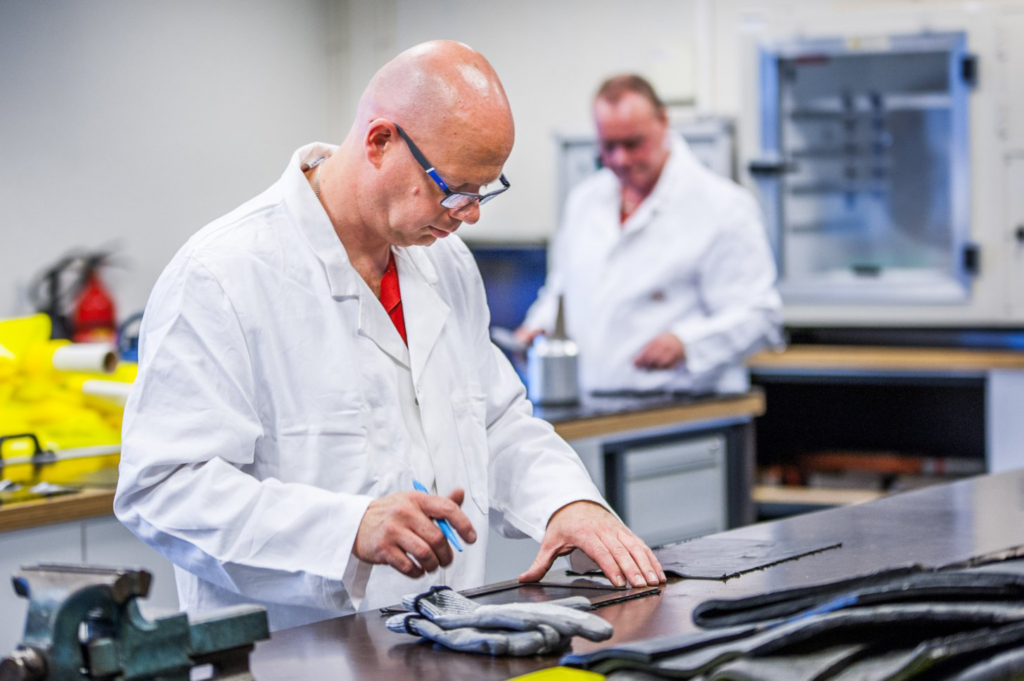
Comparison testing
Testing samples of belt made by our competitors is a routine part of the work carried out in the lab. This kind of testing provides a factual, scientific insight that helps us keep ahead of our competitors. We need to know the strengths and advantages of our belts and how they compare to the competition. With cut-price imported belting from the Far East, primarily China, continuing to swamp the market, quality and value comparison is more important than ever. Those who believe that they are saving money are actually paying a much bigger price than they realise, as these summaries of recently tested imported belt confirms:
Far East import EP630/4. 6 + 3 T3 ISO 4195 Heat resistant. This belt was sold under false pretences. It was NOT heat resistant and it did NOT have the claimed EP (polyester/nylon) carcass. It was also NOT ozone resistant.
Far East import EP 800/4 7 + 2 DIN W Abrasion resistant. This belt was specified and supplied as a 630/4 but was actually an 800/4. Cover properties did NOT meet DIN W standard in terms of abrasion resistance, tensile strength and tear strength. The tensile strength of the cover was actually below DIN Z, which is the lowest standard. The belt was NOT ozone resistant. The tested belt is not only significantly below Dunlop standards but is inadequate for purpose.
Far East import EP 1000/4 7 + 2 DIN W Abrasion resistant. This 1000 N/mm belt had an 800 N/mm fabric carcass and therefore failed to meet its claimed specification. The rubber covers were far below DIN W requirements and therefore failed to meet the claimed specification. The belt was NOT ozone resistant. This belt has clearly been supplied under false pretences and is unsuitable for the intended purpose.
Far East import 400/3 4+2 MOR Oil Resistant. The complete absence of resistance to oils and greases, full polyester carcass rather than the claimed EP and an almost total absence of ozone resistance mean that this belt does not meet claimed expectations and is unfit for purpose.
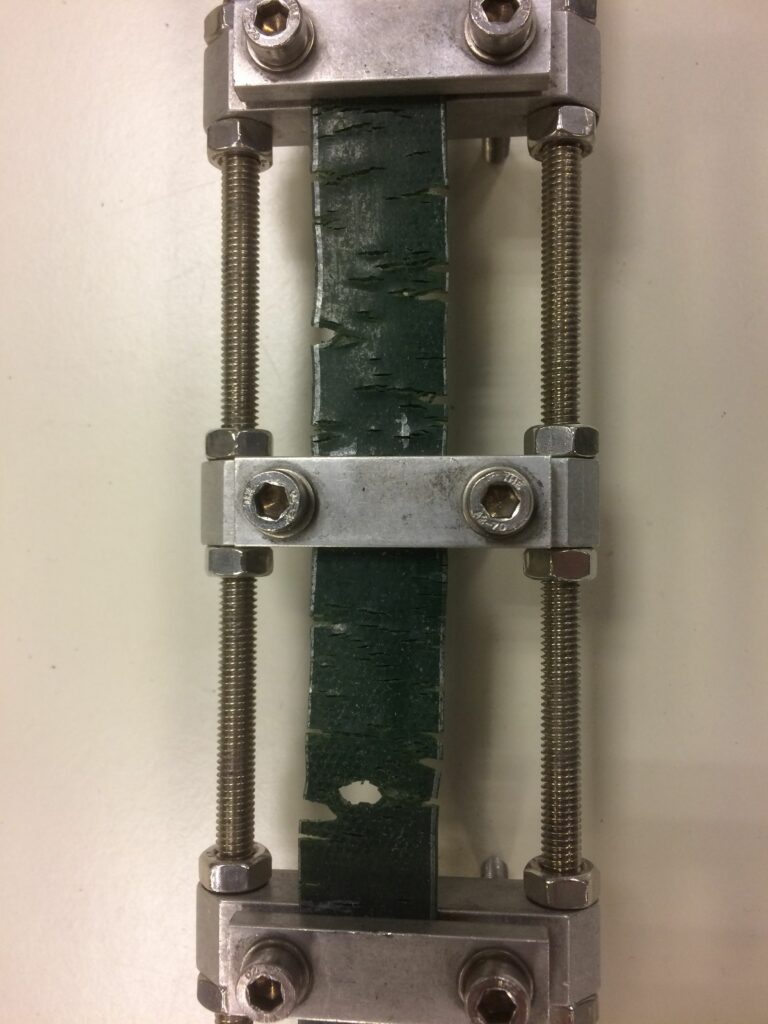
Learning the hard way.
When a large company in Germany thought that they could save some money by buying an EP 630/4 4 + 2 DIN Y abrasion resistant belt from a ‘local’ manufacturer rather that was ‘cheaper’ than the Fenner Dunlop belt they had been offered, they discovered the hard way that there was a good reason for the price difference. They very soon realized that they had quite some issues with the performance of the belt so they provided a sample of the ‘economy’ belt for laboratory testing. Here is a summary of the test findings:
Belt properties: Testing revealed that the fabric plies of the belt carcass were entirely polyester (EE) rather than the claimed specification polyester/nylon mix (EP). The elongation was extremely low (0.62%), which causes serious compression in the carcass resulting in delamination between the fabric plies and carcass tears are likely to occur after only a limited time. Also, the adhesion levels were below DIN/ISO minimum requirements, being another serious cause of carcass delamination and therefore premature failure of the belt.
Covers: Cover properties were exceptionally bad with almost non-existent abrasion resistance (325 Mm3) and not complying at all with the cover grade specification sold to the customer on paper. Tensile strength, tear strength and elongation at break were also totally insufficient, simply caused by using the minimum possible amount of polymers and using cheap fillers such as clay instead.
Ozone resistance: The cover started to crack within only 8 hours exposure of the total test time of 96 hours exposure static ozone resistance testing (EN ISO 1431/1 procedure B). This is a very poor performance and will result in premature cracking of the covers and loss of physical properties when the belt is in use.
Conclusion: This belt ranks amongst the very worst we have tested for a very long time. The supplier is a trading/service company that claims to sell good quality products. This belt is almost certainly coming from a manufacturer in the Far East and apart from the colour, it does not comply at all with what a customer should reasonably expect.
At Fenner Dunlop Conveyor Belting we test competitor samples on a very regular basis. It is never our intention to use our findings to ‘name and shame’ on our findings, but we wanted to share this with you to show what is going on in our world. End-users are not able to test the products themselves and rely on the honesty of the supplier of the belts. As you can see from the above, the actual quality of what is supplied very often differs from what they should expect.
If you want to know more or if you have serious doubts about the belts you have been supplied, please feel free to contact us directly and we will try to assist where we can. +31 512 585 555 or https://www.fennerdunlopemea.com/contact-form/