A Question of Adhesion
The critical importance of good adhesion in rubber ply conveyor belts.
Although the technical term ‘adhesion’ is well known within conveyor belt engineering circles, it is rarely mentioned and very unlikely to be taken into consideration by buyers and operators of conveyor belts. This is despite the fact that the adhesion properties are a critical influence on both performance and longevity of any ply construction rubber conveyor belt. Here is how and why:
What is adhesion?
Rubber belts with ‘multi-ply’ textile reinforcement are the most commonly used type of industrial conveyor belt. They are made up of two elements. The carcass is effectively the backbone of the belt because it provides the inherent characteristics such as its tensile strength and elongation (elasticity or ‘stretch’ under tension). The construction of the carcass consists of a single or multiple layers of extremely strong but flexible synthetic fabric ply such as polyester and nylon. These are covered by a thin ‘skim’ of rubber that bonds them together. Different rubber compounds are used for the covers and skim, although in some cases the polymers may be the same. Usually, different fillers are used to create the skim rubber. In order to increase the adhesion, the fabrics are pre-treated with a specialized coating because, without this treatment, the fabrics are too smooth and too resistant to effectively absorb the polymer, elastomer or rubber in a manner that achieves acceptable ply adhesion.
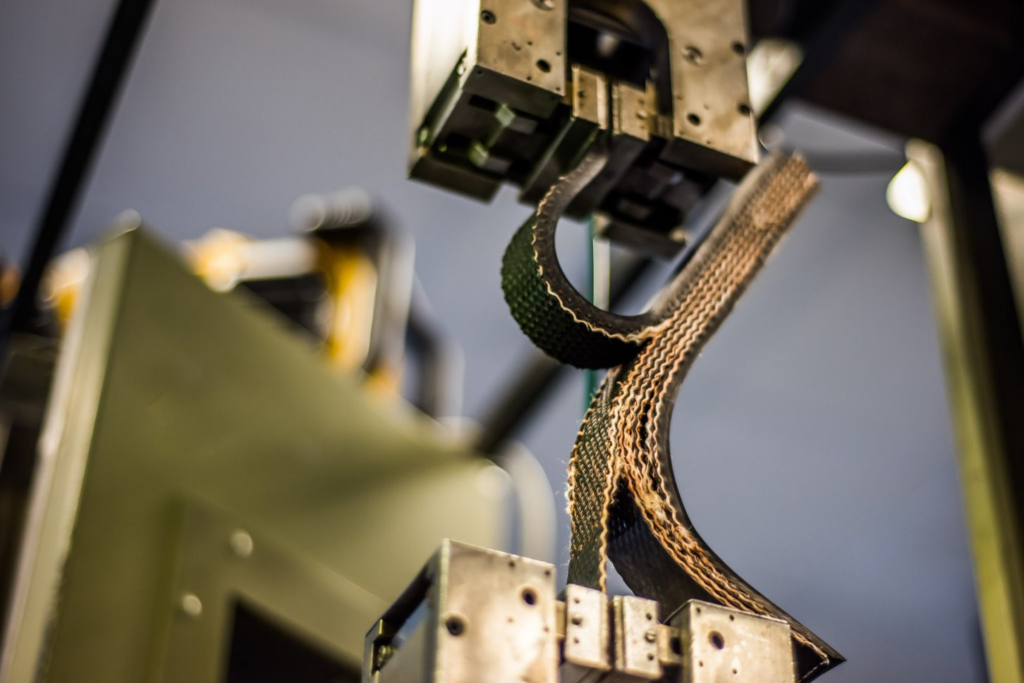
An outer cover of rubber protects the belt carcass. The term ‘adhesion’ when used in relation to conveyor belts is the adhesive bond between the inner ply layers to adjoining layers and between the surfaces of the outer plies and the rubber covers. It is defined as the force required to separate (pull apart) the adhesion between adjoining plies and/or between the plies and the outer covers. This is usually measured in Newtons per millimeter (N/mm).
Why are adhesion levels important?
Adhesion between the plies and the covers is fundamental to the durability, functionality and structural integrity of a conveyor belt. Conveyor belts continually flex over pulleys and drums. This repeated flexing action will stress the ply adhesion of conveyor belts. It is therefore essential for long-term durability that the belt has adequate ply adhesion to withstand this stress without delaminating, which is where the various layers separate and the belt begins to fall apart.
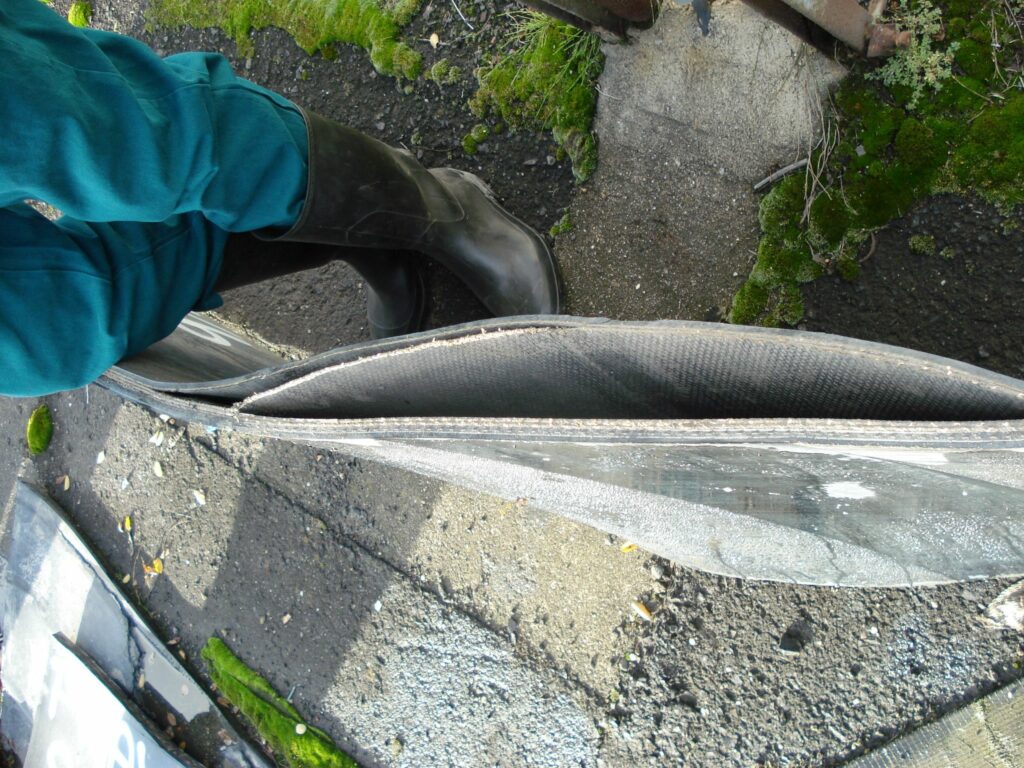
Good adhesion also helps the belt resist adverse environmental conditions, such as extreme temperatures and humidity, as well as enhancing the belt’s ability to trough and carry heavy loads without the risk of ply separation, making it suitable for more demanding applications.
Having the optimum level of adhesion has an enormous impact on the creation and ongoing reliability of splice joints. Adhesion levels that are too high can cause significant problems in the making of both hot and cold vulcanised joints. At the opposite end of the scale, and far more commonplace, is an inadequate level of adhesion because this compromises the strength of the joint, even when the workmanship has been of the highest standard. Unreliable splice joints are a very common cause of unplanned stoppages to carry out repairs.
Causes of poor adhesion
There are several reasons why a belt can have inadequate adhesion properties. As with nearly all other inadequacies in conveyor belts, the root cause is the use of low-grade (low cost) raw materials, the quality of the rubber and other cost-cutting methods used to manufacture so-called ‘economy’ belts. Low grade ingredients such as polymers, fillers such as carbon black, vulcanizing agents, plasticisers, resins and curatives all have a negative impact on adhesion levels. Other causes include moisture ingress, overheating or overcooking during the vulcanization process, poor or non-compliant rubber formulation in combination with the fabric coating and the use of bulking fillers such as chalk or clay. Another factor is the type and quality of the fabric treatment itself, which plays an essential role in both short and long-term adhesion.
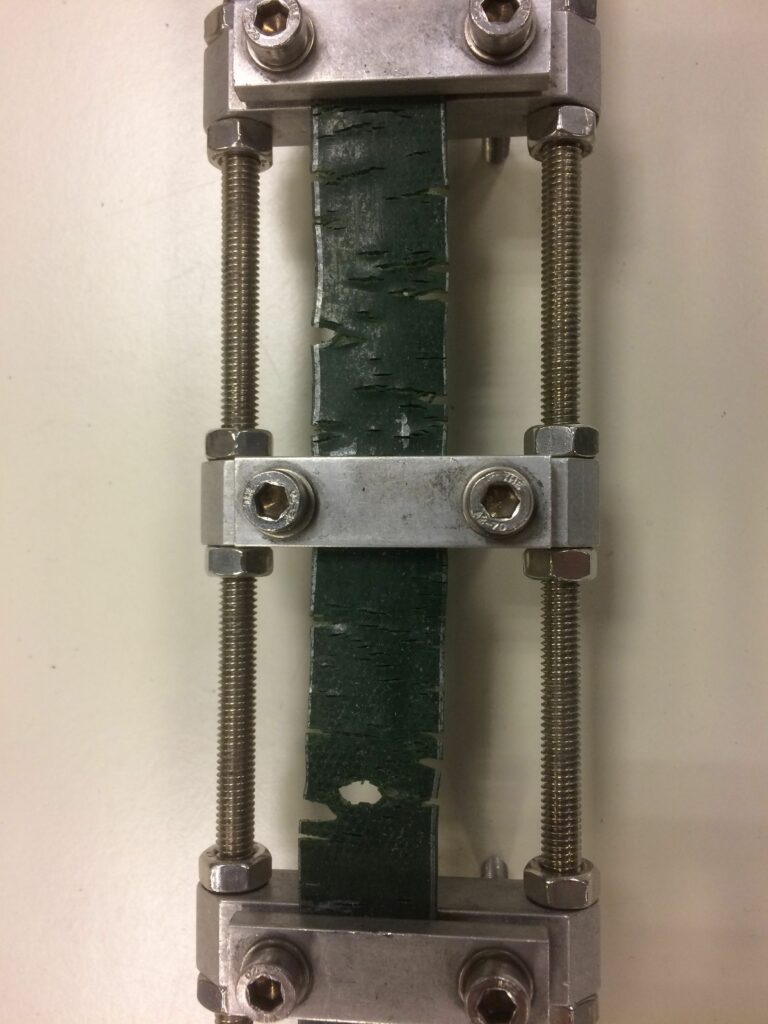
Another common ‘short-cut’ is the omission of antioxidants in the rubber compound that create resistance to the damaging effects of exposure to ground level ozone and ultraviolet light. Tests reveal that up to 90% of the rubber belts used in Europe and Africa are not resistant, despite the fact that ozone and UV significantly accelerates the oxidation of rubber, resulting in its premature degradation and loss of mechanical strength. Over time, this also makes re-splicing increasingly difficult as the adhesion properties of the rubber diminish. Exposure to ozone and UV also has a damaging effect on bare synthetic fabrics.
With so much to get right, and with so much that can go wrong, it is hardly surprising that adhesion plays such a central role in the operating life of a conveyor belt. Compromises in the pursuit of a price advantage serve only to benefit the manufacturer, never the end-user.